When a regenerative medicine startup included his company’s orifice restrictor to control the flow rate of a liquid in its production process, John Hayden started asking around about other companies in the nascent biofabrication industry.
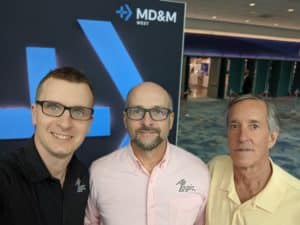
Doug Robertson, director of research at Clippard Instrument Laboratory, suggested Hayden check out the Advanced Regenerative Manufacturing Institute (ARMI) and its BioFabUSA program, of which Clippard is a member. Hayden, product development engineer and marketing manager at Air
Logic, did just that. He also joined BioFabUSA and traveled to Manchester, NH, to attend his first in-person event in early June: the Spring 2022 Meeting in the Millyard.
“The conference I was at last week was exceedingly interesting and amazing, and I was blown away,” Hayden said. “There’s so much optimism at ARMI about the problems they’re solving, the progress they’re making, and it hit me how much that stands out.”
While there, Hayden was understandably drawn to conversations with representatives from other manufacturing-related companies.
“We all had a similar opinion where this is the birth of an industry,” he said. “We want to help, we want to be a part of this both because it’s super interesting and for the long-term opportunity from a business perspective.”
While biofabrication is an emerging industry, Air Logic has years of experience and success in making pneumatic and fluidic products work in all different types of applications.
“We can help with the challenges that the group is facing in the process of growing tissues,” Hayden said. “We can help standardize variables and bring down the costs of production.”
Air Logic’s inception was in 1975, when its parent company, Knapp Manufacturing, acquired the fluidics division of Johnson Controls. In 1993, three employees—Jay Haertel, John Boticki and David Horvath—bought Knapp and the Air Logic division from the family-owners. Haertel, Boticki and Horvath remain the owners.
About 100 people work at the company’s 75,000-square-foot headquarters and production building in Racine, Wisc., where Air Logic has complete control of its process for designing and making off-the-shelf and custom fittings, check valves, filters and orifices for air and fluid control.
“Our name is Air Logic but we do all sorts of air and also liquid applications,” Hayden said. “Typically, when you have tubing in your device you need fittings, check valves, filters and orifices.”
The company operates in a number of industries adjacent to biofabrication, including analytical and medical equipment.
Because of its expertise in ventilator parts, Air Logic pitched in at the beginning of the Covid-19 pandemic and in 2020 made millions of parts for breathing machines around the globe, Hayden said.
“Every employee at our company knew we were making life-saving equipment and took special pride in that knowledge,” he said. “Even my competitors and I were working on the same projects. People were sharing drawings and technical information you never would have shared with another manufacturer. It was interesting to get the same feeling both in the shop and externally.”
At a previous company before he joined Air Logic in 2017, Hayden dealt with capital equipment for mixing epoxy, which gives him insight into the processing needs of ARMI | BioFabUSA and its members.
“You have to know if the stuff you’re doing at every stage of the game is working or not,” he said. “You can’t wait until the very end to know if you’re successful. So I was super interested in the sensor development they’re working on because I think that’s going to make or break this whole thing.”
As it turns out, the work at ARMI | BioFabUSA may end up benefiting Hayden’s own family. His mother, sister and other family members have bicuspid aortic valves due to congenital disease. The aortic valve should have three leaflets, but a bicuspid valve has only two. As a result, Hayden’s mom—who is in her mid-60s and paints en plein air as a hobby—has shortness of breath and fatigue, among other symptoms.
Seeing what goes on at ARMI | BioFabUSA inspired a spark of hope in Hayden, though.
“Seeing what they’re doing with lungs and kidneys and livers, it’s like, ‘Why not a valve?” he said.
Hayden estimated one-quarter of the speakers at ARMI |BioFabUSA’s recent meeting also had personal tales about family members who might benefit from the institute’s work.
“It just gets to your humanity,” he said. “We all have a story about people who need help.”